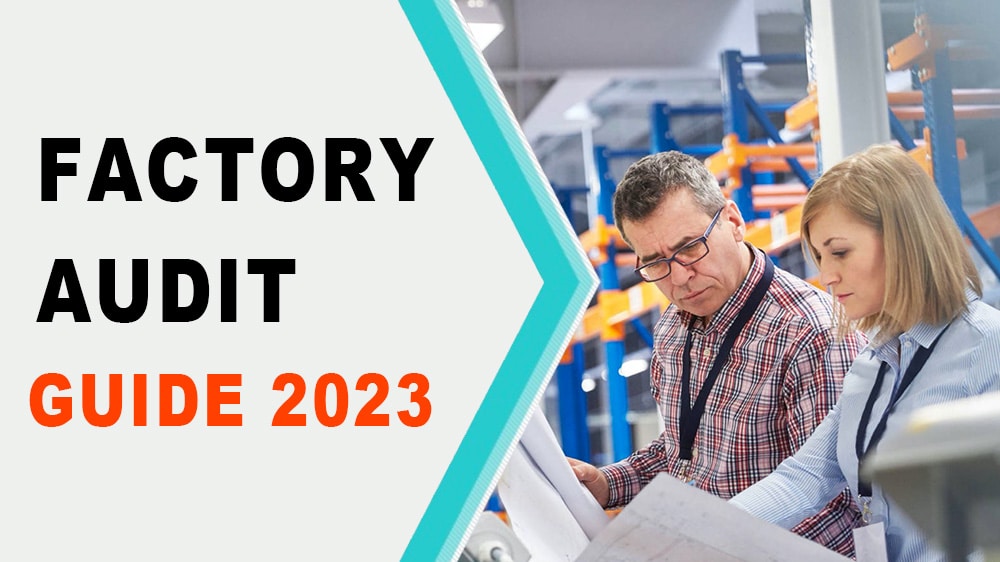
Whether you’re considering a new supplier or have been working with them for some time, it’s critical to vet them as thoroughly as possible.
A factory audit can help you ensure that your supply chain is compliant, efficient, and able to deliver quality products to your customers.
What is a factory audit, and how does it work?
In this article, we’ll answer these questions to help you better understand if a factory audit is a suitable tool for you.
What Is a Factory Audit?
A factory audit is an on-site assessment of a facility where the auditor evaluates its systems, capabilities, and workplace environment to ensure that they meet your requirements as a buyer and that the supplier provides quality services and products.
A factory audit will assess productivity. For example, a reliable supplier should deliver products on time and meet order quantities.
They should check all workflows in the production process, track how much time is spent to produce the finished product, and assess the efficiency of the machines and manufacturing equipment used.
During the factory audit, an auditor (either you, a colleague or a third-party professional auditor) will visit the factory.
After arriving, the auditor will gather information about the factory and work through a checklist of items the factory should comply with.
At last, the auditor will document all findings in a report so that you will comprehensively understand your suppliers.
It will ensure their ability to produce products according to your expectations and prevent time-consuming and costly delays.
Why Is Performing Factory Audit So Important for Importers?
Performing a factory audit can ensure that suppliers have sufficient capacity to produce products and deliver orders on time. It includes:
- The workforce is fully trained to design and build products.
- The raw materials are of good quality.
- The costs are in line with market prices.
- All of these ensure the supplier can deliver the correct order at the right time.
Performing a factory audit can greatly benefit your import business, which has the following benefits:
- Avoid encountering scams or illegal factories.
- Ensure you work with partners who can provide the highest quality products and services.
- Ensure you save time and money in dealing with the right factory.
Suppliers’ permanence and willingness to cooperate are essential to optimize business growth. A perfect plan with a flawed supplier line can cripple a business. That’s why it’s important to perform a factory audit.
What Is the Difference Between Factory Audit and Quality Inspection?
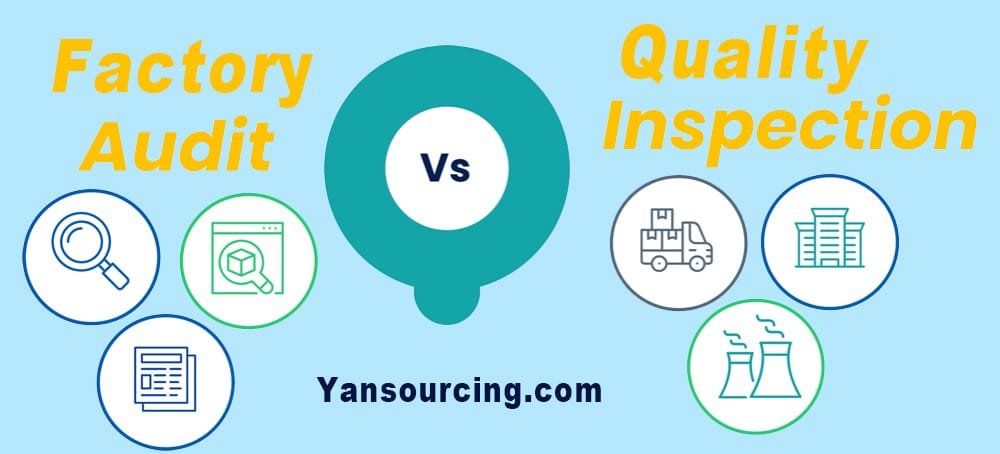
Usually, a factory audit is the final step in the sourcing process, performed after a group of potential suppliers has been selected.It is not only the most expensive form of evaluating suppliers, but it is also the most in-depth.
On the other hand, quality inspection refers to measures directed at inspecting, measuring, and testing various product characteristics and correlating the results with the requirements to comply with the required regulations.
The following are the main differences between factory audits and quality inspections:
1. Factory audit focus on the long term
When considering a different supplier to produce your product, a factory audit is helpful for you in choosing a long-term supplier.
It focuses on the quality of the maintained product, while quality inspection only focuses on the products in a particular shipment.
2. Factory audit focus on the big picture
A factory audit gives you a big picture view of how a factory operates and how it can ensure that they produce a high-quality product.
You can look at their ability to do this throughout multiple shipments, whereas a quality inspection is only for one specific shipment.
3. Factory audit is not just about product quality
Factory audit ensures that the factory meets standards related to health and safety, child labor, working hours, and management.
Buyer access to these audits can help make better supplier choices. However, quality inspection is usually performed on the factories with who you already have an established relationship.
When Should a Factory Audit be Performed?
Performing a factory audit is as expensive as it is time-consuming, so when should you perform one?
In the right balance, a factory audit can help you proactively understand a factory’s setup, performance, and key points of compliance with international standards.
So, you can perform a factory audit in the following situations:
1. New partner supplier
If you have a new supplier, doing a factory audit with this supplier is an excellent opportunity, which could be an important factor in determining whether you will work with it.
If your supplier has changed ownership or you see some differences in the quality of their work, there are hints that it may be time to audit their factory.
2. Product Complexity
When a product is more complex, more things can go wrong. So during this process, you may need to perform factory audits more frequently to ensure everything is working correctly.
3. Perform factory audits regularly
Normally, a factory audit once a year is most reasonable.
Of course, some large companies may perform a review once every three months or six months, depending on the company’s needs.
4. New regulations or requirements are introduced
Product quality starts with choosing the right supplier.
A factory audit aims to assess whether the factory has the relevant product knowledge and can produce products that meet international regulations and your brand requirements.
5. Random factory audit is not a bad idea
Sometimes your gut tells you something isn’t right, or it’s just been a while since no audited your supplier.
Then try to listen to your inner voice, which will give you peace of mind and ensure that everything goes well with your suppliers.
How to Perform a Proper Factory Audit?
There is no standard approach to performing a factory audit, and the breadth and depth of the audit will vary depending on the product or process.
But either way, a factory audit will help you find the answers to the following two basic questions:
- Does the factory have the capacity to produce the products you need?
- Does the factory have the ability to fulfill orders on time?
There are some key steps to performing a factory audit correctly.
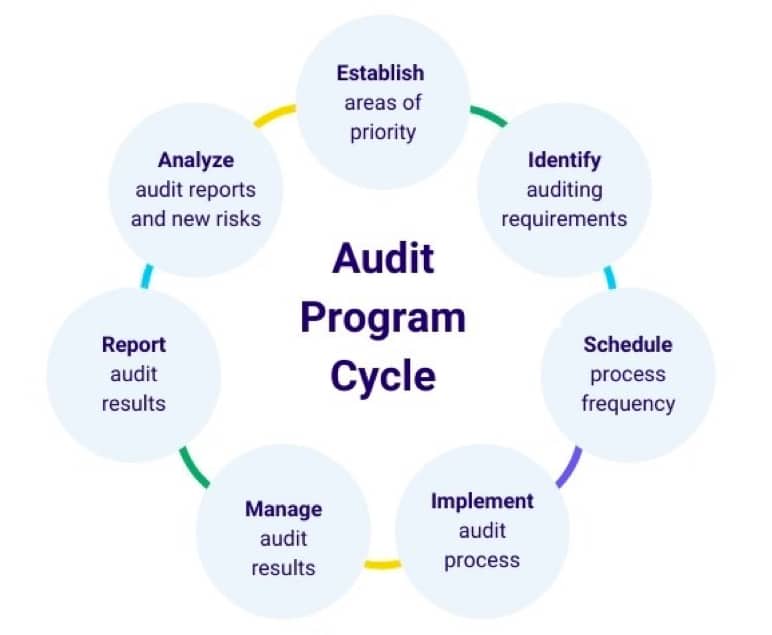
Here’s a checklist of everything you need to do to learn how to audit your suppliers:
Step 1: Pre-audit data collection.
A successful factory audit begins with the preparation of data before the audit. This process includes collecting, organizing, and analyzing all relevant data to help develop the audit’s type, duration, scope, and specific objectives.
A well-structured and comprehensive pre-audit questionnaire can be a valuable tool for obtaining pre-audit information.
Step 2: Select the type of audit.
How to audit the factory, you must determine the focus and objectives you want to achieve through the audit.
Here, you can choose one of the following 3 audit types that best meet your specific goals:
Quality audit
The auditor will follow a checklist loosely based on the ISO 9000 series.
He typically observes verification of incoming materials, in-process and finished goods. The goal is to find gaps in the factory’s quality system and assess its reliability.
Social compliance audit
The auditor will check if the factory respects the regulations of its country and some other standards, such as SA 8000 or ISO 26000.
The verification focuses on payroll records, worker interviews, observations on the shop floor, etc.
Security audit
It will ensure that the factory meets the required safety in packaging and transportation.
In addition, it will confirm that the factory is not in contact with unauthorized organizations and companies dealing with illegal items and substances.
Step 3: List tasks and perform an audit.
Depending on the type of audit you need, perform specific tasks to measure the performance and effectiveness of specific areas accurately.
When performing an audit, list each task in a series of steps. Make sure to follow each step to ensure that nothing is missed.
Step 4: Audit report generation
When the audit is complete, ask your auditor to create an audit report that documents all of their findings.
The audit report serves as written evidence that the audit occurred, and any deficiencies are documented.
Step 5: Follow-up
The auditor should develop a follow-up action plan to ensure that corrective actions are implemented and verified as effective on time.
In addition, a re-audit should be scheduled to confirm that critical remediation of all material weaknesses has been completed.
A successfully performed factory audit will identify, resolve, and prevent problems in supplier product quality or processes before they spread, ensuring that suppliers consistently meet quality expectations.
7 Common Types of Factory audits
1. Internal quality system audit
This type of audit is an examination of the tools used to measure quality itself. Internal quality audits assess an organization’s electronic quality management system (EQMS).
The quality documentation and processes managed by the software solution are reviewed to ensure maximum efficiency and high-quality product results.
Software manuals are reviewed to ensure that all key areas of the solution are covered and that the document is readily accessible to all key employees.
Work instructions are audited to ensure compliance with standard operating procedures and confirm that quality processes meet goals.
2. Manufacturing audit
During a manufacturing audit, the auditor determines whether the supplier is capable of the following:
- Produce the products that meet your company’s specifications.
- Resolve costly disruptions.
- Prevent additional costly disruptions after production has begun.
A manufacturing audit can bring you some benefits like:
- Verify that your supplier’s production facilities are suitable for producing your product.
- Ensure that your company’s purchasing policies are consistent with your suppliers.
- Identify and reduce potential quality, operational and ethical risks.
- Evaluate the capabilities of factory management.
3. Supplier Audit
Supplier audits allow companies to work directly with suppliers in real-time. By auditing the supply chain, companies can control the quality of their suppliers and sub-suppliers and introduce accountability for poor performance.
Key performance indicators (KPIs) can quickly identify areas for improvement.
With such transparency, suppliers can view purchase order activity, such as receipt and inspection history, to collaborate on non-conformances and corrective actions.
4. Structural Audit
A structural audit is performed to analyze the integrity and safety of your suppliers’ buildings and premises.
This includes auditing structural integrity, fire safety measures, and relevant codes and conditions.
Performing a structural audit can:
- Ensure safe working conditions, which can help prevent minor and catastrophic injuries.
- Ensure that employee health is not at risk.
- Protect your brand image and reputation.
- Review compliance with statutory requirements.
- Help to gain an accurate understanding of the security situation in your supply chain.
- Prevent supply chain disruptions.
5. Security Audit
A security audit looks at the programs and procedures designed to protect the safety of your company’s employees.
This audit can include reviewing equipment operations or examining organizational procedures to ensure day-to-day safety.
Successful safety policies can prevent injuries and accidents and improve the overall well-being of employees.
6. Environmental Audit
An environmental audit is designed to help companies create a safer work environment, help identify areas of risk in the workplace, and develop actionable plans to meet OSHA and other standards.
The audit ensures that employees comply with regulatory standards and use appropriate personal protective equipment.
By monitoring and improving the environmental impact of your supply chain, environmental factory audits help assess compliance with local laws and regulations related to environmental protection.
7. Risk Evaluation Audit
Risk evaluation is a process of identifying potential hazards in the workplace and then classifying each risk so that preventive measures can be put in place. This type of audit helps companies put effective risk mitigation strategies into place.
Preventive measures can be prioritized when all risks have been identified to prevent adverse workplace and economic results.
Factory Audit Checklist
The factory operating conditions may be similar, but no two factories are the same regarding arrangement, output, and staffing.
When developing a new factory audit checklist, it may be helpful to refer to a general template for factory audits.
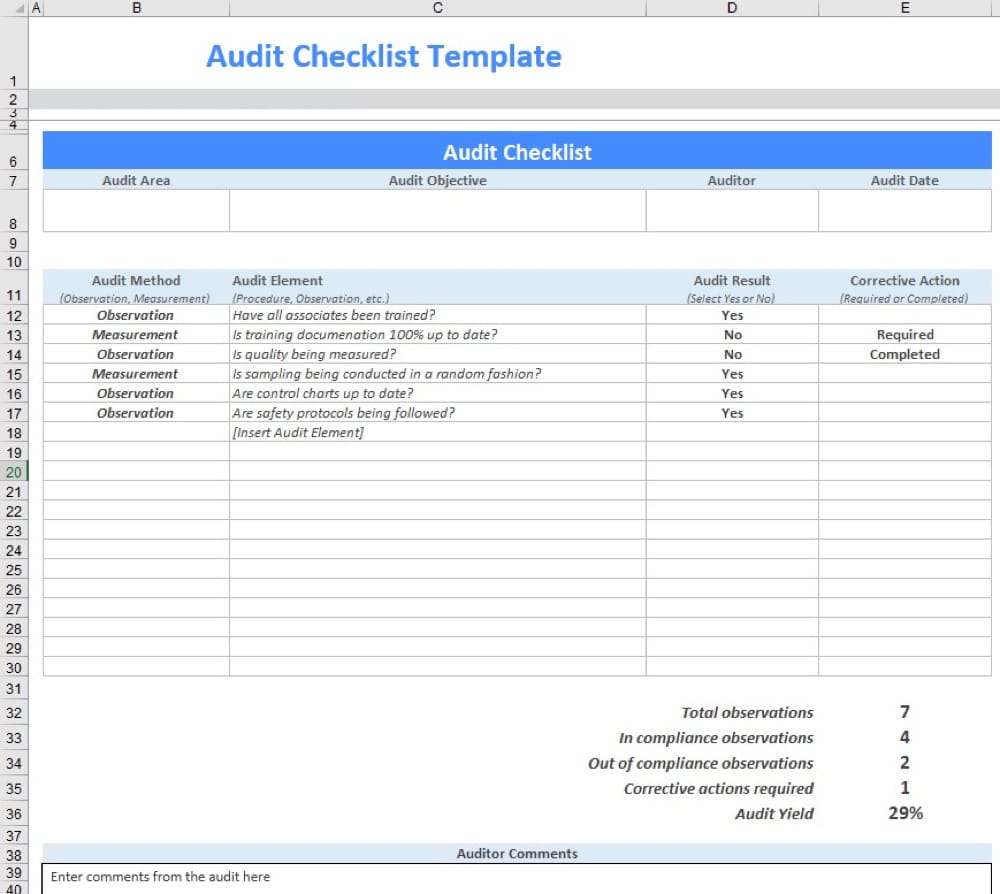
This template can be used as a guide for auditors doing the following:
- Provide general information about the suppliers.
- Assess all key areas, such as production, quality, and compliance.
- Take photo evidence of any risks that need to be addressed immediately.
- Assign actions to responsible teams and authorized personnel.
- Determine if the supplier being evaluated can assist your business.
- Complete the audit by signing off on it.
How Yansourcing Help You Do Factory Audit in China?
Yansourcing knows well the importance of having a quality, efficient and compliant supply chain, which is why we offer a strong factory audit service.
Yansourcing’s factory audit minimizes risk and provides an accurate snapshot of your suppliers. We want to ensure your success in delivering quality products to your customers promptly and safely.
Yansourcing’s auditors will perform a factory visit to assess all processes’ reliability, legality, and capability.
We can provide you with a detailed factory audit via live video and can also provide you with all the documentation to keep you in the loop.
We offer factory audits and quality inspections for Amazon, eBay, and other e-commerce industries. Please contact us, and we’ll help you with the rest.
Factory Audit Conclusion
As an importer, dealing with the right suppliers is an important prerequisite to obtaining quality products that meet your specifications and customers’ expectations.
Performing regular factory audits of your suppliers and developing corrective action plans is invaluable in encouraging continuous improvement in your supplier facilities.
As a result of this guide, you now understand that factory audit is the most critical factor. In addition, we have learned how quality inspections are different from factory audits.
To learn more now, contact Yansourcing at +86 15902071989 (Whatsapp) or email info@yansourcing.com.