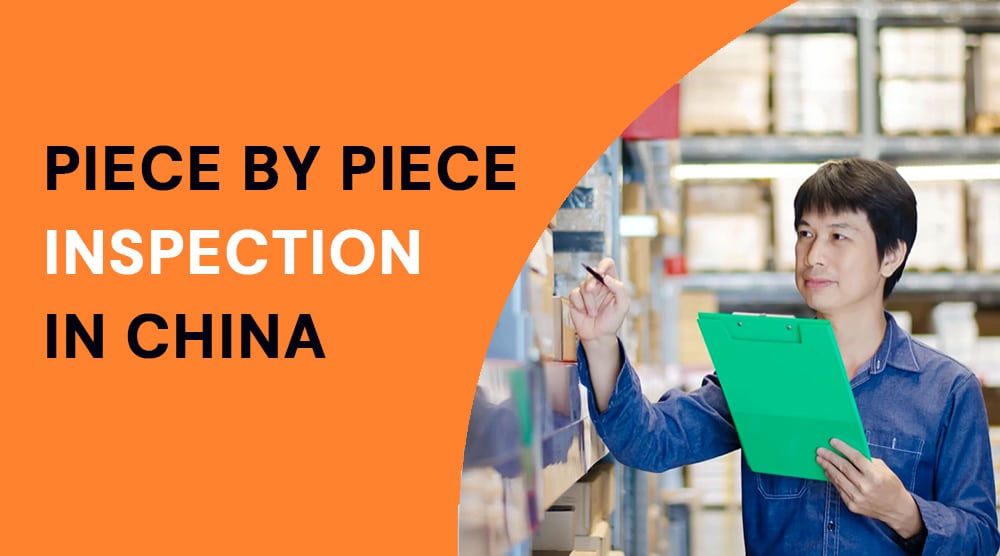
Are you importing goods from China and worried about maintaining the highest quality standards?
Piece by piece inspection is a proven method that ensures your products meet the desired specifications and quality requirements.
This comprehensive guide will walk you through the importance of quality control in China, the process of piece by piece inspection, factors to consider when selecting an inspection company, and alternatives to piece by piece inspection.
The Importance of Quality Control in China
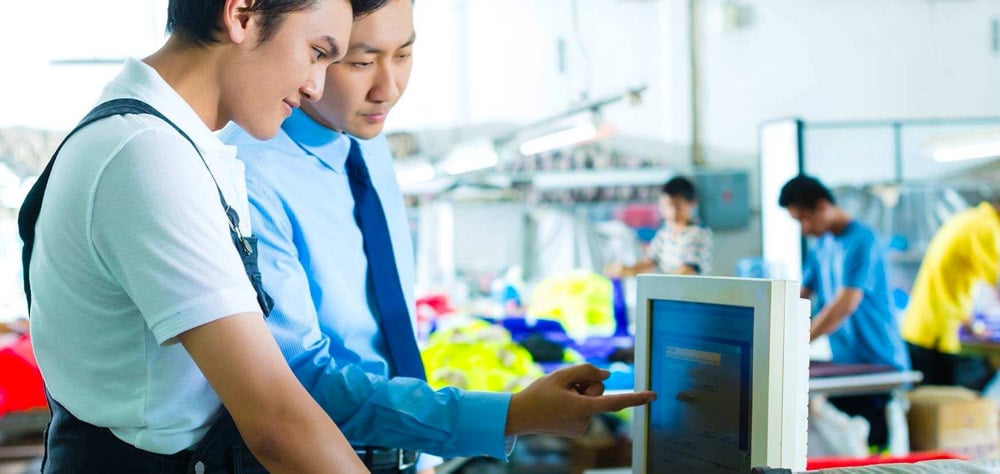
1. The role of quality control in international trade
Quality control is crucial in international trade, especially when dealing with products manufactured in China.
With the country being a global manufacturing hub, ensuring that the products you import are of high quality is paramount to protect your investment and satisfy your customers.
2. Ensuring customer satisfaction
Customer satisfaction is key to the success of any business.
By implementing strict quality control measures like piece by piece inspection, you ensure that your customers receive top-quality products, which results in positive reviews and increased customer loyalty.
3. Protecting your brand reputation
Poor quality products can tarnish your brand’s reputation, leading to negative reviews, loss of customers, and reduced revenue.
Implementing piece by piece inspection helps protect your brand by guaranteeing that the products you import from China meet the required standards.
4. Maintaining a Competitive Edge
In today’s global market, competition is fierce.
To maintain a competitive edge, it’s essential to ensure the products you import from China are of high quality.
Implementing rigorous quality control measures, like piece by piece inspection, can help you stay ahead of your competitors.
5. Reducing the Risk of Product Recalls
Product recalls can be costly and damaging to a company’s reputation.
By conducting piece by piece inspection, you can significantly reduce the risk of recalls due to product defects or non-compliance with safety regulations.
6. Compliance with International Regulations and Standards
Many industries have specific regulations and standards that must be adhered to, such as the European Union’s CE marking or the US’s FDA regulations.
Piece by piece inspection can help ensure your products meet these requirements and avoid potential legal issues.
Understanding Piece by Piece Inspection
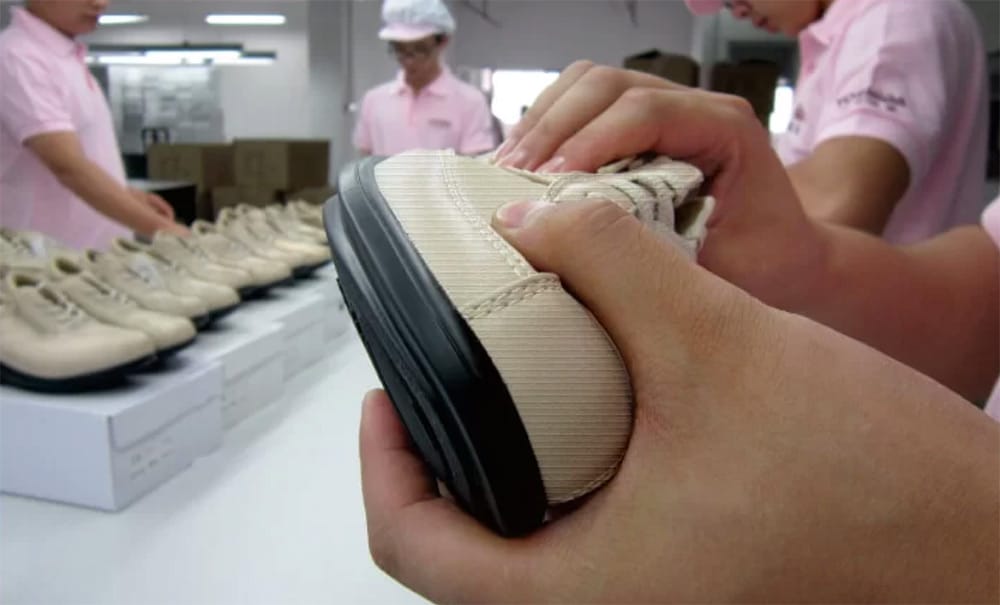
1. Definition and scope
Piece by piece inspection, also known as 100% inspection, is a quality control method that involves inspecting every single item in a production batch.
This method is typically used for high-value products, small production runs, or when product quality is of utmost importance.
2. When to use piece by piece inspection
Piece by piece inspection is appropriate in situations where:
- The product is complex and requires thorough examination.
- The cost of a defective product is high.
- The risk of non-compliance with regulations or standards is significant.
3. Benefits of piece by piece inspection
Here are some of the benefits of this type of inspection:
- Ensures that all products meet the required quality standards.
- Minimizes the risk of defective products reaching customers.
- Provides valuable feedback to manufacturers for continuous improvement.
4. Limitations of piece by piece Inspection
While piece by piece inspection offers many benefits, it’s essential to be aware of its limitations.
Inspectors may not catch every single defect, especially in cases where defects are not immediately visible.
Additionally, piece by piece inspection can’t guarantee that future production batches will be of the same quality, as factors like manufacturing processes and supplier performance may change over time.
Piece by Piece Inspection Process
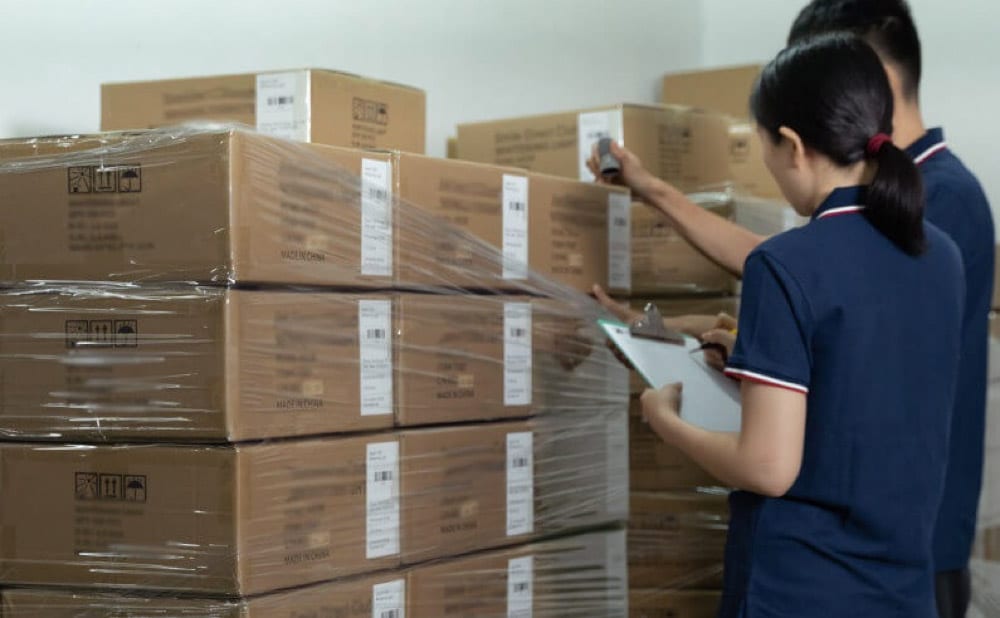
1. Pre-production inspection
Before production begins, inspectors assess raw materials, components, and machinery to ensure they meet the required standards.
This step helps identify any potential issues before they affect the final product.
2. In-process inspection
During production, inspectors monitor the manufacturing process to ensure compliance with specifications and quality requirements.
They identify any deviations from the set standards and provide timely feedback to the manufacturer for corrective action.
3. Final inspection
Once production is complete, a piece by piece inspection is conducted on every item.
Inspectors check for defects, non-conformities, and adherence to specifications.
Any issues identified are reported to the manufacturer for rectification before shipment.
4. Container loading supervision
Inspectors oversee the loading process, ensuring that products are packed correctly and safely for transportation.
This step helps prevent damage during transit and verifies that the correct items and quantities are being shipped.
5. Post-inspection Follow-up
After the final inspection, it’s crucial to follow up with the manufacturer to address any issues found during the inspection process.
This may include negotiating compensation, requesting rework or replacement of defective products, or implementing corrective actions to prevent future issues.
Factors to Consider When Choosing an Inspection Company
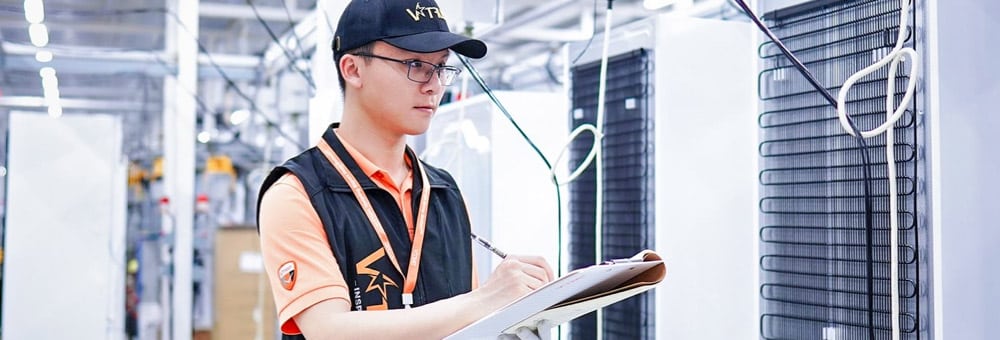
1. Experience and expertise
Select a company with extensive experience in inspecting products similar to yours.
An experienced inspection company will have a deep understanding of the quality requirements and standards for your specific industry.
2. Transparency and communication
Choose a company that provides clear and transparent communication throughout the inspection process.
Regular updates and detailed reports will help you stay informed and make well-informed decisions.
3. Pricing and services
Consider the pricing and range of services offered by the inspection company.
Make sure they provide comprehensive inspection services at competitive rates.
4. Certifications and Accreditations
Look for inspection companies with relevant certifications and accreditations, such as ISO 9001, which demonstrates their commitment to quality management systems and continuous improvement.
Challenges of Piece by Piece Inspection
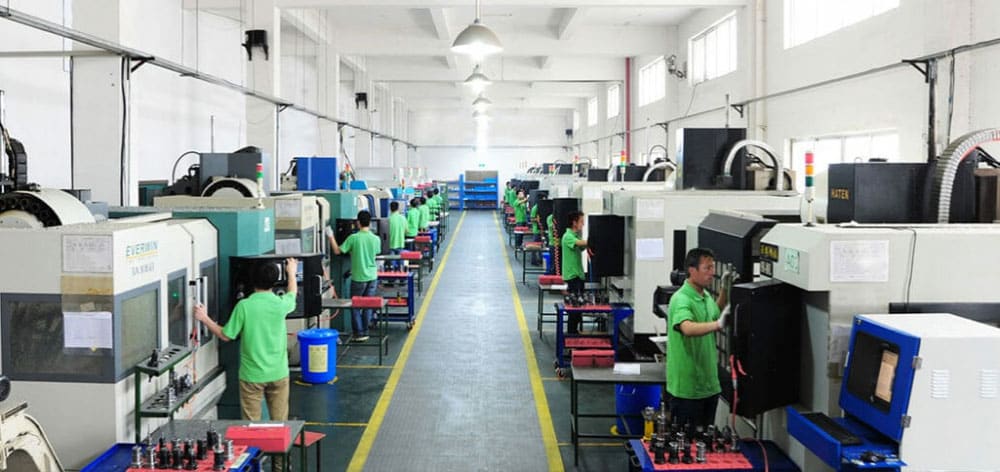
1. Time-consuming process
Inspecting each item in a production batch can be time-consuming, especially for large orders.
This may cause delays in shipment and increase lead times.
2. Increased costs
Piece by piece inspection can be more expensive than other inspection methods due to the labor-intensive nature of the process.
3. Finding qualified inspectors
Finding and retaining qualified inspectors who can consistently and accurately assess product quality can be challenging, particularly in remote locations.
4. Balancing Inspection Rigor with Cost and Efficiency
While piece by piece inspection provides the highest level of quality assurance, it’s essential to balance the rigor of the inspection process with cost and efficiency.
In some cases, a combination of piece by piece inspection and other quality control methods, such as random sampling or in-house quality control, may be more appropriate.
Alternatives to Piece by Piece Inspection
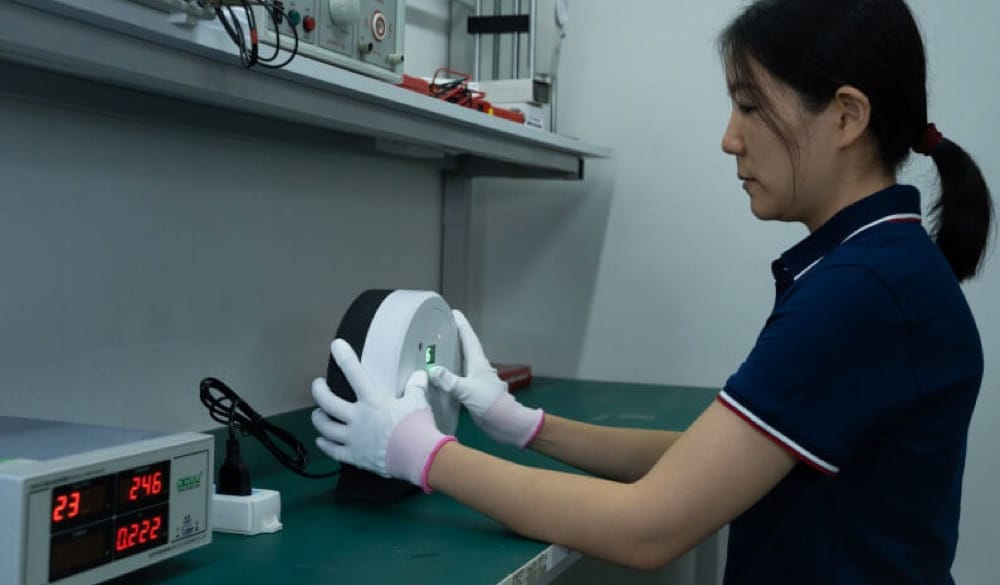
1. Random sampling inspection
Instead of inspecting every item, random sampling involves selecting a representative sample of the products for inspection.
This method is faster and more cost-effective but may not be suitable for products with a high risk of defects.
2. 100% inspection
In some cases, a 100% inspection of specific critical components or aspects of the product may be more appropriate than a piece by piece inspection.
This approach focuses on areas of greatest risk while still offering a high level of quality assurance.
3. In-house quality control
Some businesses choose to establish their own in-house quality control teams to oversee the production process and conduct inspections.
This approach allows for greater control over the inspection process but requires investment in personnel and training.
4. Pre-shipment Inspection
Pre-shipment inspection involves examining a representative sample of the final products before they are shipped.
This method can identify defects or non-conformities but may not provide the same level of assurance as piece by piece inspection, especially for high-risk products.
Case Studies of Successful Piece by Piece Inspections
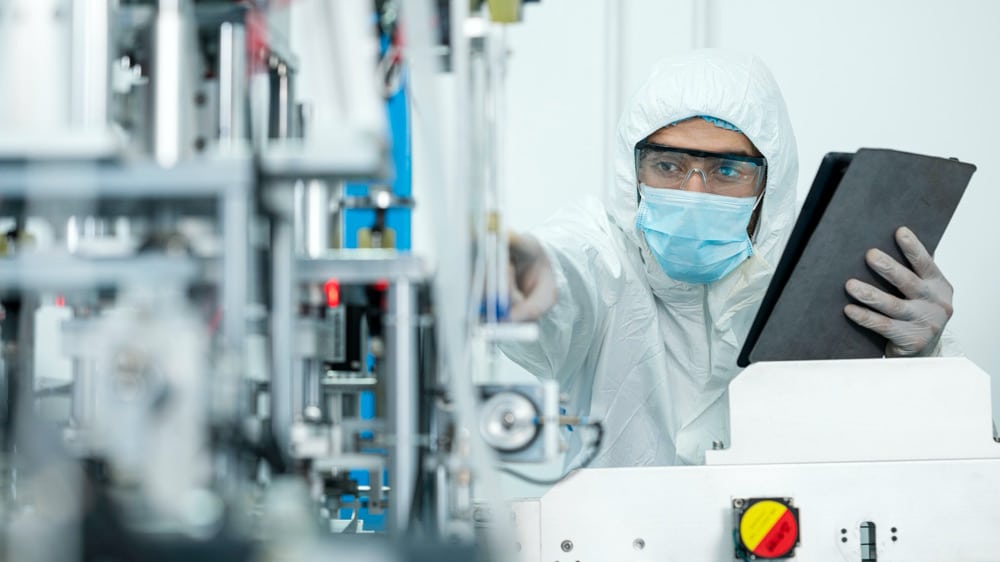
1. Electronics industry
A major electronics company implemented piece by piece inspection to ensure the quality of their high-end audio equipment.
As a result, they saw a significant reduction in customer complaints and product returns, leading to increased customer satisfaction and loyalty.
2. Textile industry
A luxury fashion brand conducted piece by piece inspections on their garments to maintain the highest quality standards.
This approach helped them maintain their reputation for excellence and attract high-end clientele.
3. Toy industry
A leading toy manufacturer used piece by piece inspection to ensure the safety and quality of their products, meeting strict international regulations and avoiding costly recalls.
4. Automotive Industry
A global automotive parts supplier implemented piece by piece inspection for critical components, ensuring the safety and performance of their products.
This approach led to fewer warranty claims and increased customer satisfaction.
5. Medical Device Industry
A medical device manufacturer conducted piece by piece inspections on their life-saving equipment, maintaining the highest quality standards and meeting stringent regulatory requirements.
Implementing Piece by Piece Inspection in Your Business
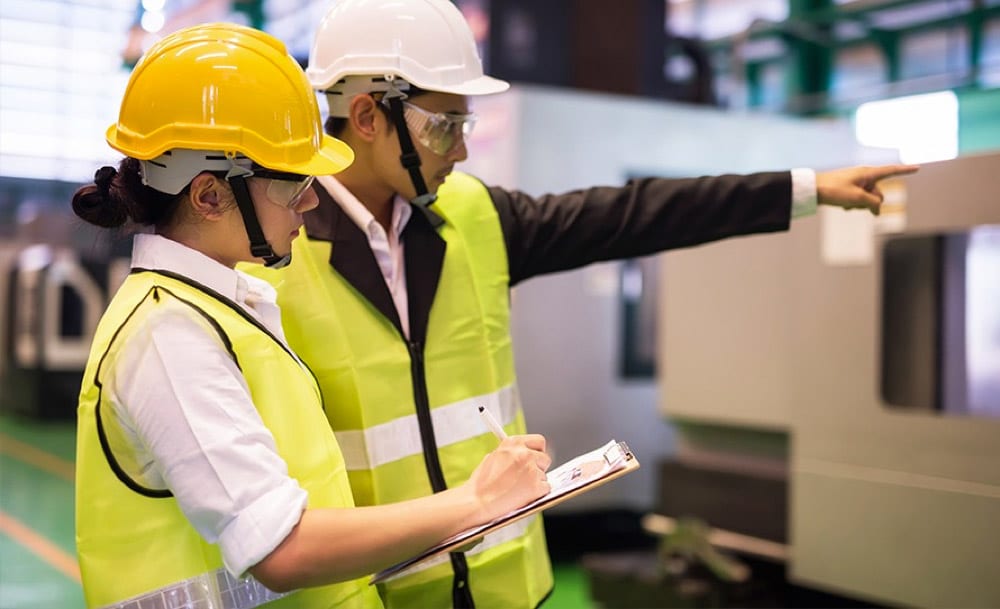
1. Establishing Quality Control Procedures
Develop a quality control plan that outlines the specific procedures and criteria for piece by piece inspection.
This plan should include details such as product specifications, defect classification, and inspection methods.
2. Training and Development
Ensure that inspectors receive proper training and development to maintain their skills and stay up-to-date with industry best practices and regulatory requirements.
3. Continuous Improvement
Use the results of piece by piece inspections to identify trends and areas for improvement.
Work closely with manufacturers to implement corrective actions and drive continuous improvement in product quality.
Leveraging Technology in Piece by Piece Inspection
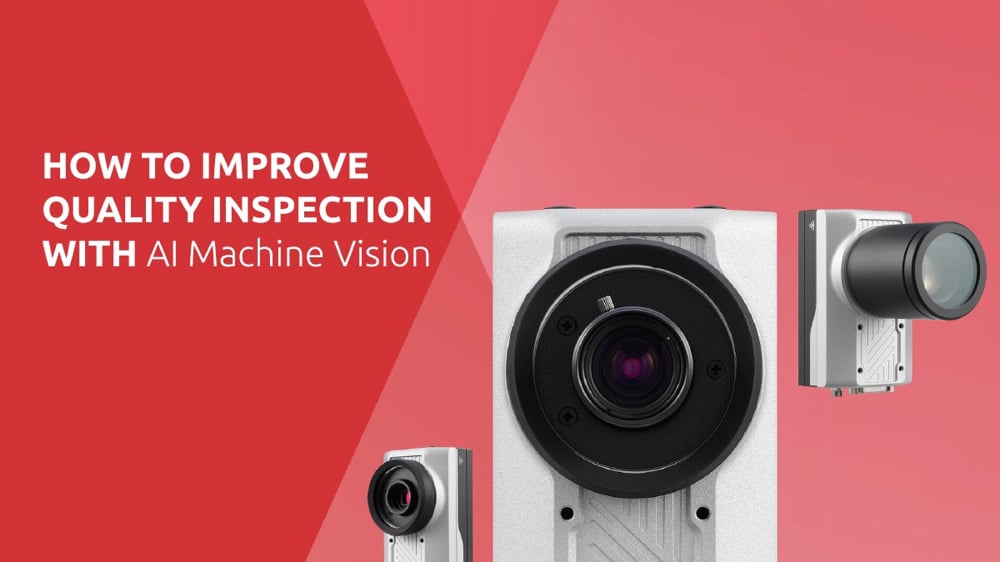
1. Digital Reporting Tools
Utilize digital reporting tools to streamline the inspection process and enhance communication between inspectors, manufacturers, and importers.
Digital reports can include photos, videos, and detailed descriptions of any issues found during the inspection, allowing for more effective decision-making and faster resolution of issues.
2. Artificial Intelligence and Machine Learning
Incorporate artificial intelligence (AI) and machine learning (ML) technologies to improve the accuracy and efficiency of piece by piece inspections.
AI-powered systems can analyze data collected during inspections, identify patterns, and provide insights for more effective quality control and continuous improvement.
3. Automated Inspection Equipment
Employ advanced automated inspection equipment, such as high-resolution cameras, sensors, and robotic systems, to increase the speed and accuracy of piece by piece inspections.
These technologies can reduce human error, minimize the time required for inspections, and lower overall inspection costs.
Working with Manufacturers to Improve Quality

1. Collaboration and Communication
Maintain open and transparent communication with your manufacturers throughout the production process.
Share your quality control requirements, inspection results, and expectations for continuous improvement.
By fostering a collaborative relationship, you can work together to achieve higher quality standards.
2. Supplier Audits
Regularly conduct supplier audits to assess the manufacturer’s quality management systems, production capabilities, and commitment to continuous improvement.
Supplier audits can help you identify potential risks, evaluate a supplier’s performance, and ensure they align with your quality control expectations.
3. Performance Metrics
Establish performance metrics to measure and track the success of your piece by piece inspection program.
These metrics can include defect rates, inspection efficiency, and overall product quality.
Use the data to identify trends, pinpoint areas for improvement, and evaluate the effectiveness of your quality control efforts.
Conclusion
Piece by piece inspection in China is an essential tool for importers looking to ensure the highest quality standards for their products.
By understanding the process, selecting the right inspection company, and implementing a comprehensive quality control plan, you can ensure that the products you import from China meet your customers’ expectations and comply with industry regulations.
As the global market continues to evolve, leveraging technology and fostering strong relationships with manufacturers will be crucial in maintaining a competitive edge and driving continuous improvement in product quality.
We are Yansourcing, a leading sourcing company in China, dedicated to helping our clients source products from China at the most competitive prices. If you are interested in importing from China, please feel free to contact us.
FAQs
1. What is the main purpose of piece by piece inspection?
The main purpose is to ensure that every product in a batch meets the required quality standards and specifications, minimizing the risk of defective products reaching customers.
2. Is piece by piece inspection suitable for all industries?
While it can be used in various industries, it’s particularly beneficial for those where product quality is of utmost importance, such as electronics, luxury goods, and products with strict safety regulations.
3. How does piece by piece inspection differ from random sampling inspection?
Piece by piece inspection involves inspecting every item in a production batch, while random sampling inspection checks a representative sample of the products.
Random sampling is faster and more cost-effective but may not be suitable for high-risk products.
4. What are some challenges of implementing piece by piece inspection?
Some challenges include the time-consuming nature of the process, increased costs, and finding qualified inspectors.
5. Are there alternatives to piece by piece inspection?
Yes, alternatives include random sampling inspection, 100% inspection of specific critical components, and establishing in-house quality control teams.
The choice depends on the specific needs and risk factors of your products.